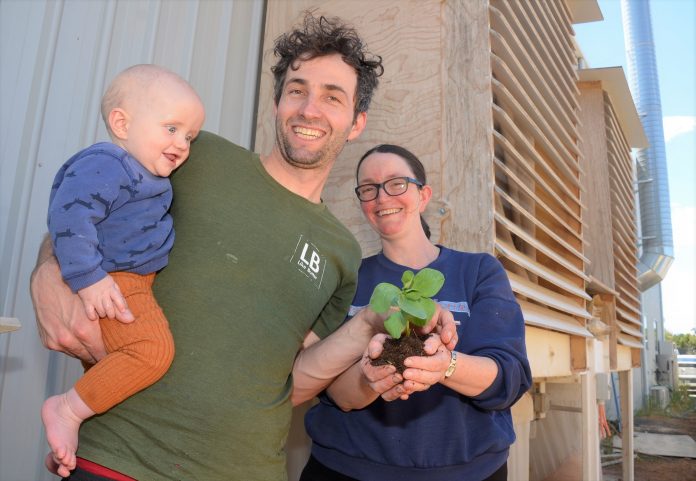
A Castlemaine business is setting a groundbreaking example by re-using its industrial waste, reducing the volume of material going to landfill and creating a valuable new product to boot.
At its factory site in Castlemaine’s Fitzgerald Close, Like Butter makes furniture and, keen to do the right thing by the environment, it recently started a trial using waste resulting from its manufacturing process to create garden compost.
Now, after many months of trialling cold composting of the waste – largely plywood sawdust but also glues – the test results are in and they’re just what Like Butter’s owners Jem Freeman and Laura Woodward had hoped for.
“We commissioned SESL Australia, a leading environmental science laboratory and consultancy service, to assess the results,” says Jem, as he scoops up a handful of the friable result, writhing with worms and ready for use.
“One of our main interests was ensuring the safe break down of the adhesives used in plywoods, particularly formaldehyde-based glues.
“Our hope was that the fungi and bacteria would work its magic and consume, digest and then churn these chemicals into something safe for the environment and ultimately for productive use.
“The tests are back and they show that we produced a good quality compost suitable for a variety of uses including ornamental gardens.
“We have a little work to do with zinc and copper levels, only limiting the compost in high yield vegetable gardens used for daily consumption.
“But because these macro nutrients are used in fertilisers, and the levels detected were only marginally above standard, it may be that they were introduced via green waste rather than workshop waste.
“The glues were the big concern so it’s a big win to know they’re breaking down safely.”
Armed with the positive report results, Laura says the next step now is to trial hot composting, potentially a far quicker process from input to end result.
“The next step is trialling hot composting to deal with volume,” she says.
“The aim is to get close to zero waste.”
The local business is particularly keen to partner with other like-minded local enterprises to further enhance its innovative recycling efforts.
“We are open to partnering with others, perhaps a high green waste organisation to match the proportions of our timber waste, bringing together the two ingredients to create a viable volume at scale,” Jem says.
While it’s still comparatively early days, what they’re doing is already being closely watched by manufacturers of other commercial goods from across Australia and further afield with enquiries in recent days including one from a cabinet-making enterprise in New Zealand.
“We’ve got 18000 Instagram followers and also through our blog post, people are definitely watching what we’re doing with interest,” Laura says.